The Latest Technology Trends in Crane Modification and Repair
- hrudd0
- May 28, 2024
- 3 min read
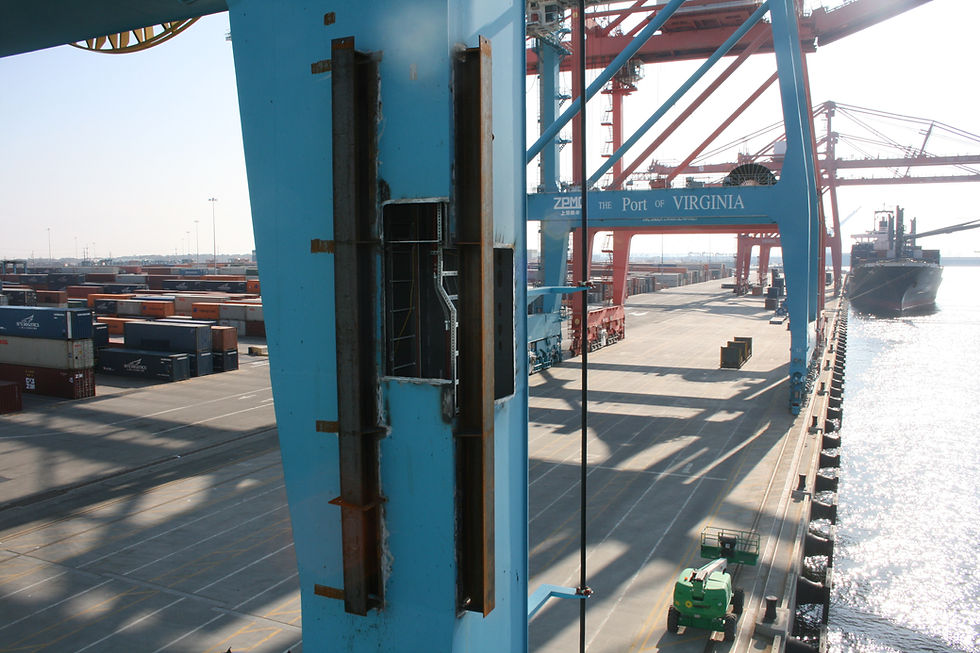
Welcome to the Global Rigging and Transport blog, where we bring you the latest insights and trends in the world of crane modification and repair. As an industry leader, we pride ourselves on staying at the forefront of technological advancements to ensure our clients benefit from the most efficient, safe, and innovative solutions. Today, we're excited to share some of the latest technology trends revolutionising the crane industry.
1. Advanced Telematics and IoT Integration
The Internet of Things (IoT) is making significant strides in crane technology. Modern cranes are now equipped with advanced telematics systems that provide real-time data on various parameters such as load weight, wind speed, and operational hours. These systems help in predictive maintenance by monitoring the condition of critical components and alerting operators to potential issues before they become major problems. This proactive approach reduces downtime and enhances safety by ensuring cranes are always in optimal working condition.
2. 3D Printing for Custom Parts
3D printing, or additive manufacturing, is transforming the way we approach crane repair and modification. The ability to create custom parts on-demand reduces lead times and allows for precise engineering adjustments. This technology is particularly useful for producing complex components that would be costly or time-consuming to manufacture using traditional methods. By leveraging 3D printing, we can enhance the performance and extend the lifespan of cranes with bespoke parts tailored to specific operational needs.
3. Augmented Reality (AR) for Maintenance and Training
Augmented reality is becoming a valuable tool in the crane industry for both maintenance and training purposes. AR can overlay digital information onto the physical world, providing technicians with detailed instructions and diagrams directly in their field of view. This technology simplifies complex repair procedures and ensures accuracy. Additionally, AR is an excellent training aid, allowing operators and technicians to gain hands-on experience in a virtual environment before working on actual equipment.
4. Remote Monitoring and Diagnostics
Remote monitoring systems have become essential for modern crane operations. These systems enable off-site technicians to monitor crane performance and diagnose issues from anywhere in the world. With remote diagnostics, problems can be identified and addressed swiftly, often without the need for an on-site visit. This capability is particularly valuable in remote or hazardous locations, where minimising downtime is critical.
5. Advanced Materials and Coatings
The development of new materials and coatings is enhancing the durability and performance of crane components. High-strength, lightweight materials such as carbon fibre composites are being used to reduce the weight of crane booms without compromising strength. Additionally, advanced coatings that provide superior resistance to corrosion and wear are extending the lifespan of critical parts, reducing the frequency of repairs and replacements.
6. Automation and Robotics
Automation and robotics are increasingly being integrated into crane operations. Automated systems can handle repetitive tasks with precision, reducing the risk of human error and increasing efficiency. Robotic arms and automated welding systems are also being used in the manufacturing and repair of crane components, ensuring consistent quality and improving production speed.
7. Predictive Analytics and Machine Learning
Predictive analytics, powered by machine learning algorithms, is revolutionising crane maintenance. By analysing vast amounts of data collected from sensors and telematics systems, these algorithms can predict when components are likely to fail and recommend timely interventions. This predictive approach not only minimises unexpected breakdowns but also optimises maintenance schedules, reducing overall operational costs.
At Global Rigging and Transport, we are committed to embracing technological advancements to provide our clients with the best possible crane modification and repair services. By staying ahead of the curve, we ensure that our solutions are not only innovative but also reliable and efficient. As the crane industry continues to evolve, we look forward to leveraging these trends to enhance safety, performance, and productivity in all our projects.
Contact us today to learn more about how we can support your crane modifications and repairs: d.close@globalrigging.com.
GRT has offices in Virginia (US), Vancouver (Canada), San Antonio (Chile) and Panama City (Panama), enabling our capacity to meet the needs of global clients quickly and efficiently.
Comments